Le Groupe Lorillard donne une nouvelle dimension à sa production bois et se dote d’une nouvelle cabine de laquage unique en France
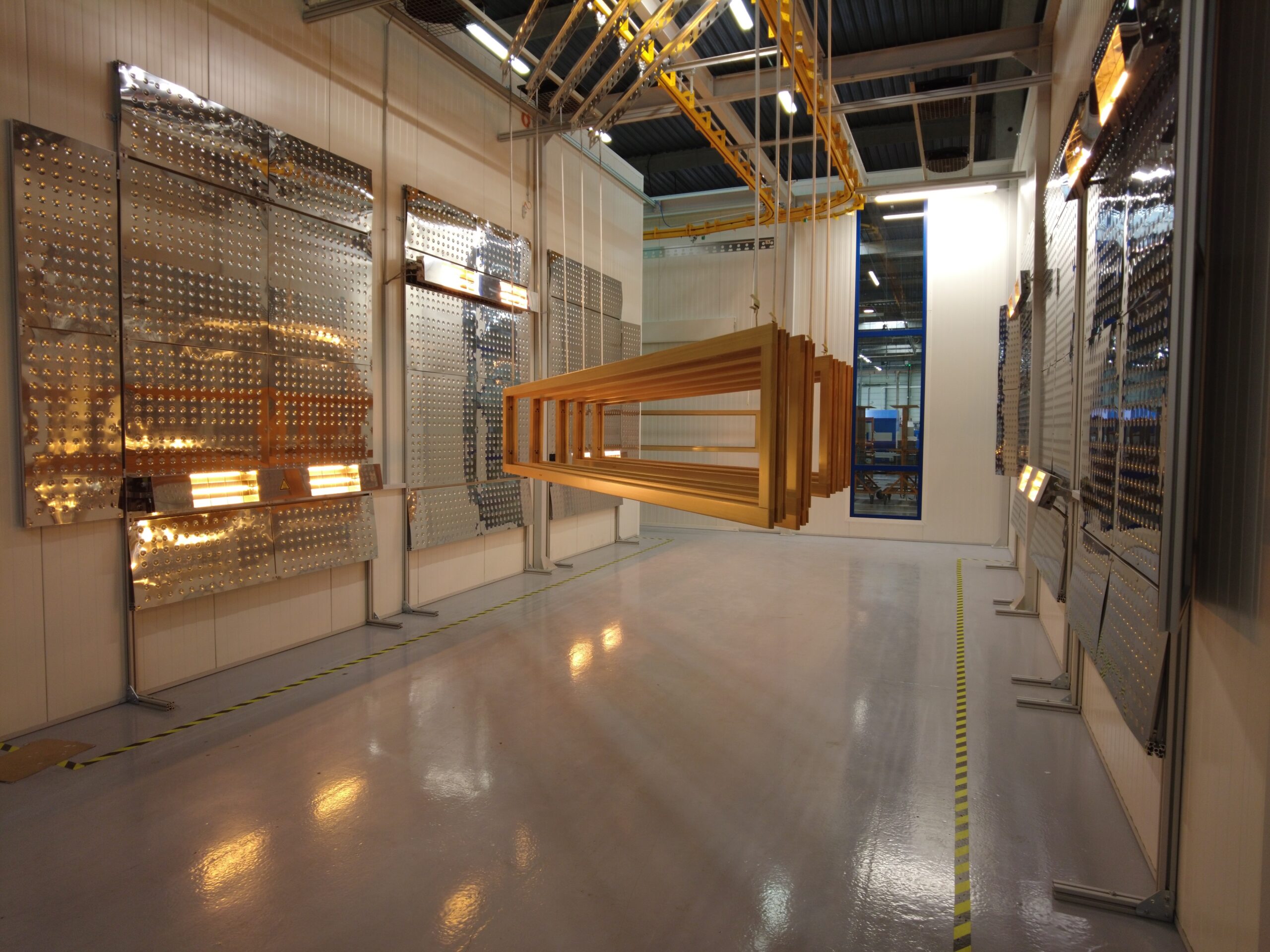
Le Groupe Lorillard qui fête ses 85 ans cette année, vient honorer cet anniversaire avec l’acquisition d’une nouvelle cabine de laquage. Outil unique et exceptionnel de par ses dimensions et sa technologie de pointe, cette cabine propulse le Groupe dans une dimension industrielle beaucoup plus ambitieuse.
Partie intégrante de son ADN, l’ambition est pour le Groupe Lorillard un argument de croissance.
85 ans plus tard, et un ADN immuable, le Groupe investit massivement – 17 millions d’euros – dans son outil de production bois pour s’assurer la position légitime de N° 1 sur ce marché en France, en matière de savoir-faire.
Cette expertise est notamment possible grâce à la singularité des moyens que le Groupe a acquis.
Pour exemple, cette nouvelle cabine de laquage est la seule, actuellement en France, capable de laquer de façon industrielle un châssis de menuiserie de 4 mètres par 3 mètres.
AUGMENTER LA CAPACITÉ DE PRODUCTION
Sur les 40 000 m² d’ateliers de l’usine de Chartres, 1000 m² sont dédiés à l’installation de la nouvelle cabine de laquage bois – contre 340 m² auparavant pour la précédente cabine – afin d’augmenter la capacité de production.
Et pour être plus précis, Thierry Luce – Président du Groupe Lorillard – explique « De 50 menuiseries bois par jour en 3-8, le Groupe est passé depuis le mois d’octobre à 90 menuiseries par jour avec ses 2 nouveaux robots et la possibilité de faire croitre la cadence à 125 menuiseries par jour avec un troisième robot. ».
Au sein de ces 1000 m², la nouvelle unité de production rassemble un système de dépoussiérage automatique par flux d’air filtré, 2 cabines de laquage robotisées dont une pour l’impression et l’autre pour la finition, 3 tunnels de séchage infrarouge, ainsi qu’un système de recyclage des boues de peintures et eaux usées.
Mais cette nouvelle cabine de laquage bois n’est que les prémices d’un projet bien plus conséquent visant à augmenter la volumétrie de fabrication des menuiseries bois.
Pour ce faire, 1,5 millions d’euros viennent également d’être investis dans la commande d’un nouveau centre d’usinage. Automatisé et robotisé, en double cabine, pour l’usinage des dormants en bois, il sera en place à l’horizon fin 2022. Puis une troisième phase d’investissement en 2023 viendra doubler la capacité de production des dormants.
TECHNOLOGIE DE POINTE
Le système automatisé et les technologies intégrées à cette nouvelle cabine offrent au Groupe une technique de laquage de qualité bien supérieure à ce qui se fait sur le marché.
L’ergonomie de la ligne avec son poste de pilotage centralisé, le scannage des menuiseries et le système de puce NFC (Near Field Communication) a intégré dans la production des notions d’instantanéité, de sécurité, d’économie, de traçabilité et d’efficacité prépondérantes pour une industrialisation de pointe.
Ainsi le scannage de la menuiserie rassemble toutes ces caractéristiques et va permettre de définir la quantité, le type et le coloris de la peinture à appliquer.
La puce NFC quant à elle, permettra de suivre étape par étape l’évolution du process de finition.
En pratique, en entrée de cabine, toutes les menuiseries sont scannées. Elles sont placées sur des balancelles qui sont, elles, équipées d’une puce NFC.
Les menuiseries sont d’abord dépoussiérées puis un premier flow-coat de préservation est appliqué par aspersion ; il permettra de préserver la menuiserie des insectes, champignons et moisissures.
Le système aiguille ensuite la menuiserie vers une zone de séchage de préservation.
Un deuxième flow-coat d’imprégnation est appliqué.
L’aiguillage se fait automatiquement en fonction des finitions souhaitées : pour une finition lasure transparente, c’est u
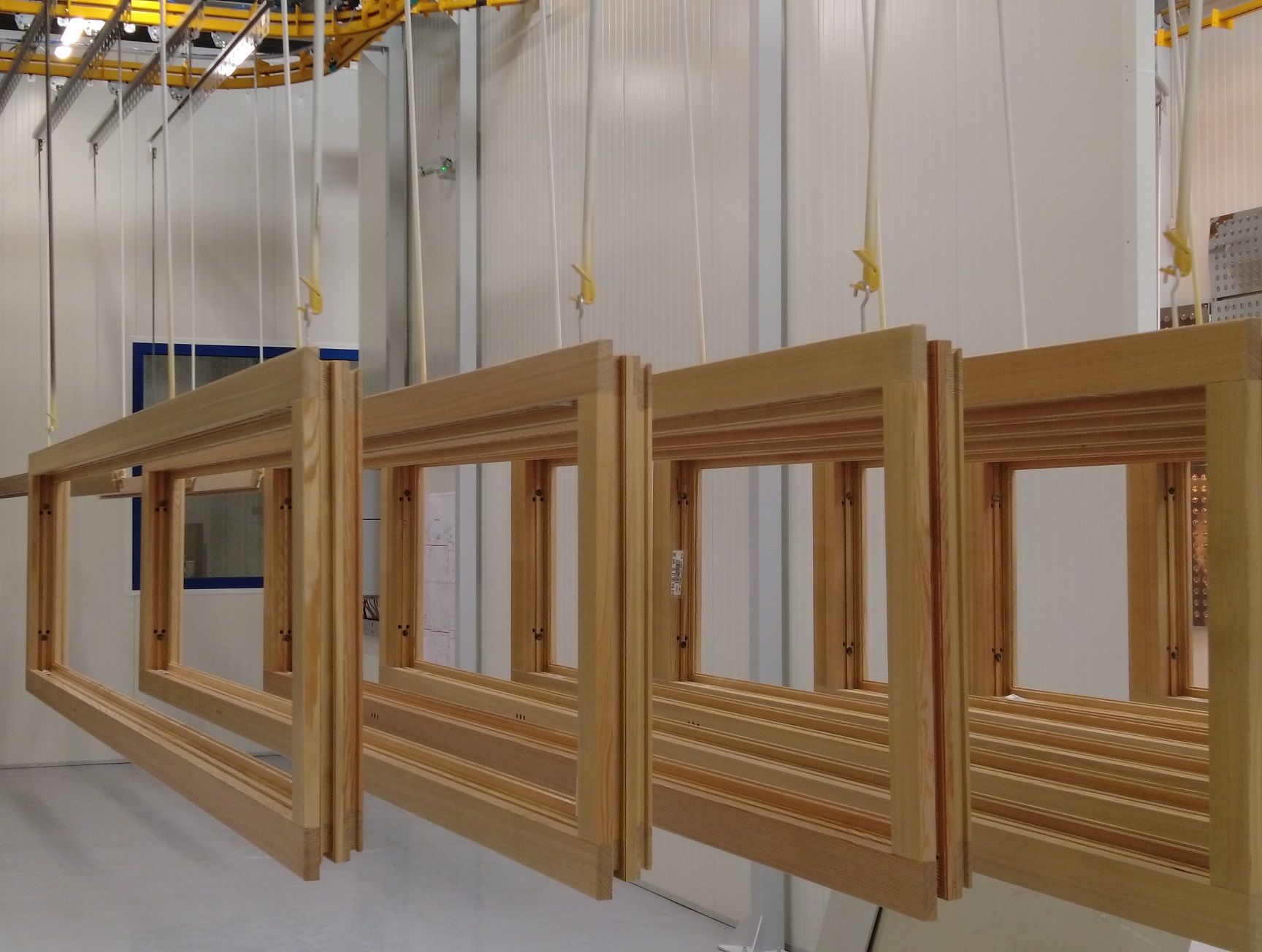
Balancelles équipées d’une puce NFC sur lesquelles sont placées les menuiseries.
Les menuiseries sont par la suite égouttées. Cette étape d’égouttage est nécessaire pour préparer les menuiseries à recevoir la teinte finale. L’hygrométrie de cette zone est notamment régulée à 60% pour permettre d’optimiser l’égouttage afin que les menuiseries ne sèchent pas trop vite.
Les boues de peintures et les eaux usées qui en proviennent sont récoltées et traitées avec un coagulant et un floculant permettant de séparer les éléments. Un filtre à charbon et un filtre à particules les nettoient avant leur rejet dans les égouts.
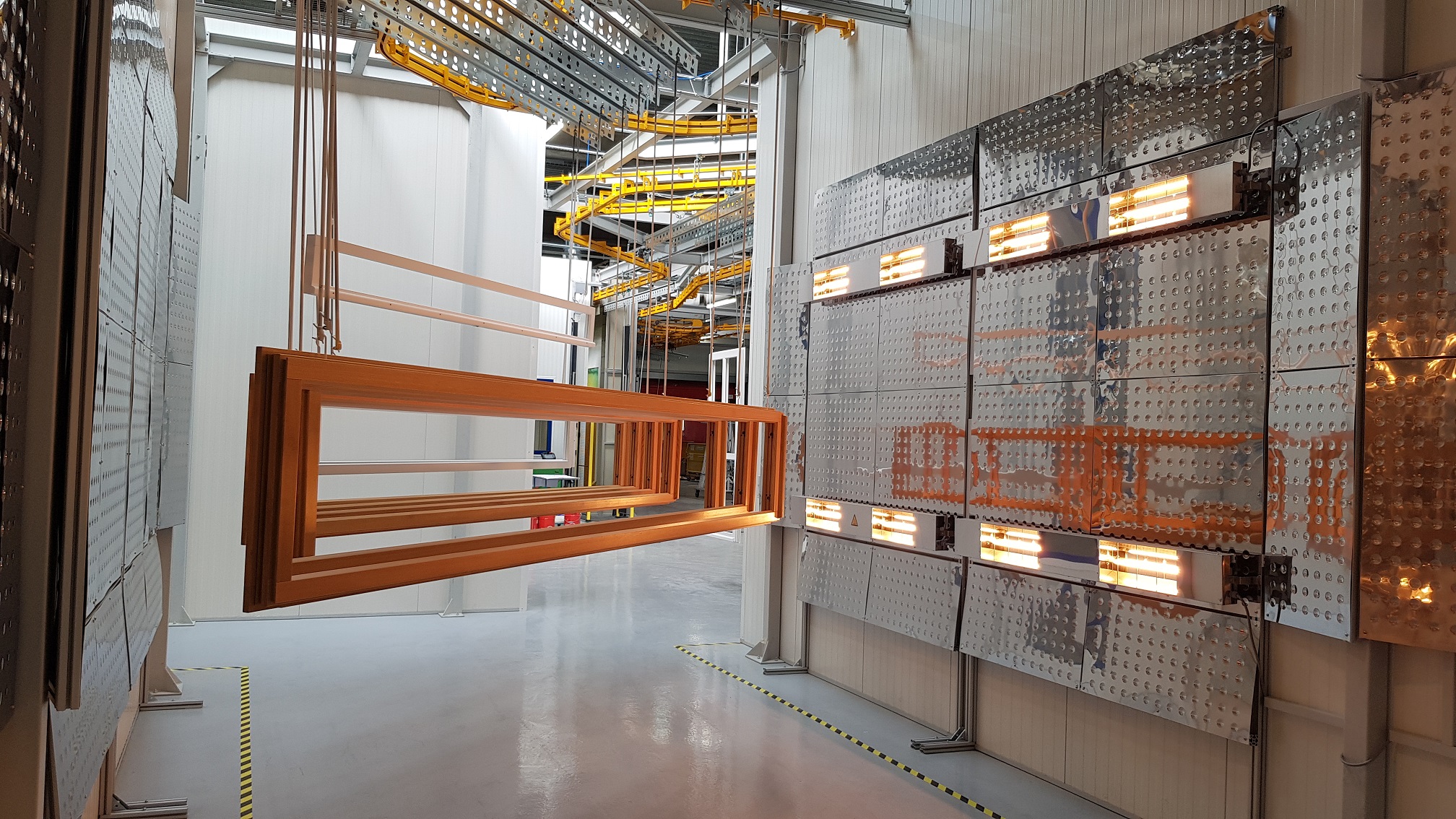
Menuiseries séchées dans un tunnel à infrarouge de 11 kW
Après égouttage, les menuiseries sont de nouveau séchées dans un tunnel à infrarouge de 11 kW (lampes halogènes). Ce séchage à coeur qui s’exécute de l’intérieur vers l’extérieur, est efficace en 30 minutes au toucher et à coeur en 1h 30.
Avec une température ambiante de 25°C, cette méthode de séchage est 3 fois moins énergivore et ne nécessite pas le refroidissement du tunnel entre chaque menuiserie.
Cette technique offre véritablement une qualité de séchage supérieure avec moins de défaut lors des manutentions ou lors des opérations sur les menuiseries après peinture. Elle autorise également la palettisation des menuiseries 6h après la sortie de la cabine, là où il fallait habituellement attendre un minimum de 12h pour éviter les phénomènes de collage entre les fenêtres.
Deux autres cabines équipées de robots sont dédiées à la pulvérisation intermédiaire et à la pulvérisation de finitions. Réalisée par des robots anthropomorphes à 6 axes, la pulvérisation est appliquée par 2 pistolets automatiques airmix. Le calcul des trajectoires est automatique et précis, et, un système de débitmètre évalue la quantité de peinture par menuiserie. Leur grande amplitude de travail les habilite à peindre des cadres de 4m par 3m.
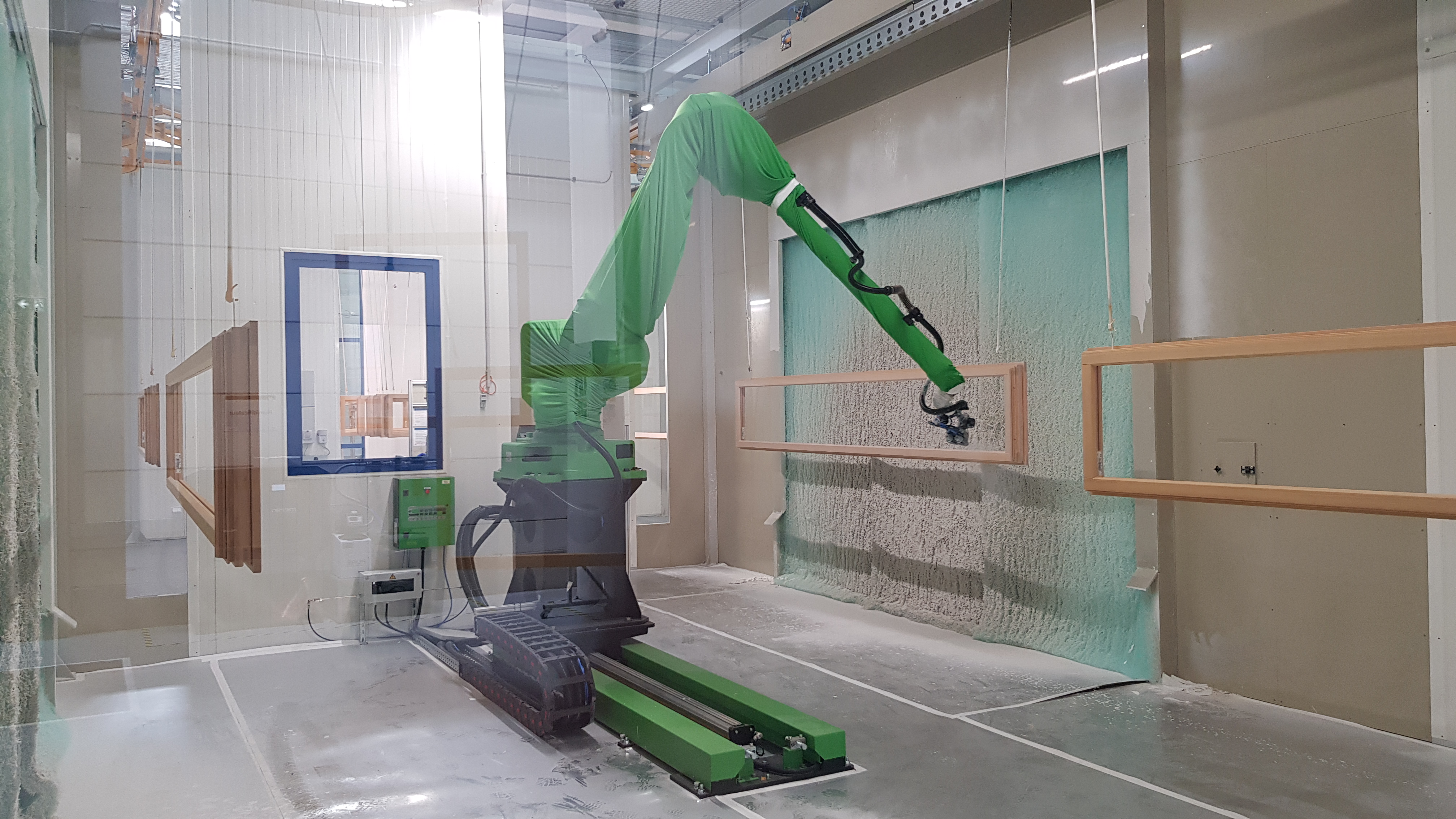
Robot anthropomorphe à 6 axes équipé de 2 pistolets automatiques airmix
2 autres tunnels de séchage infrarouge de 22 kW sont dédiés au séchage des menuiseries des cabines de pulvérisation et finition. Un contrôle qualité, réalisé par un personnel qualifié, finalise le processus de laquage qui est garanti jusqu’à 10 ans pour les finitions opaques et 5 ans pour les lasures transparentes.
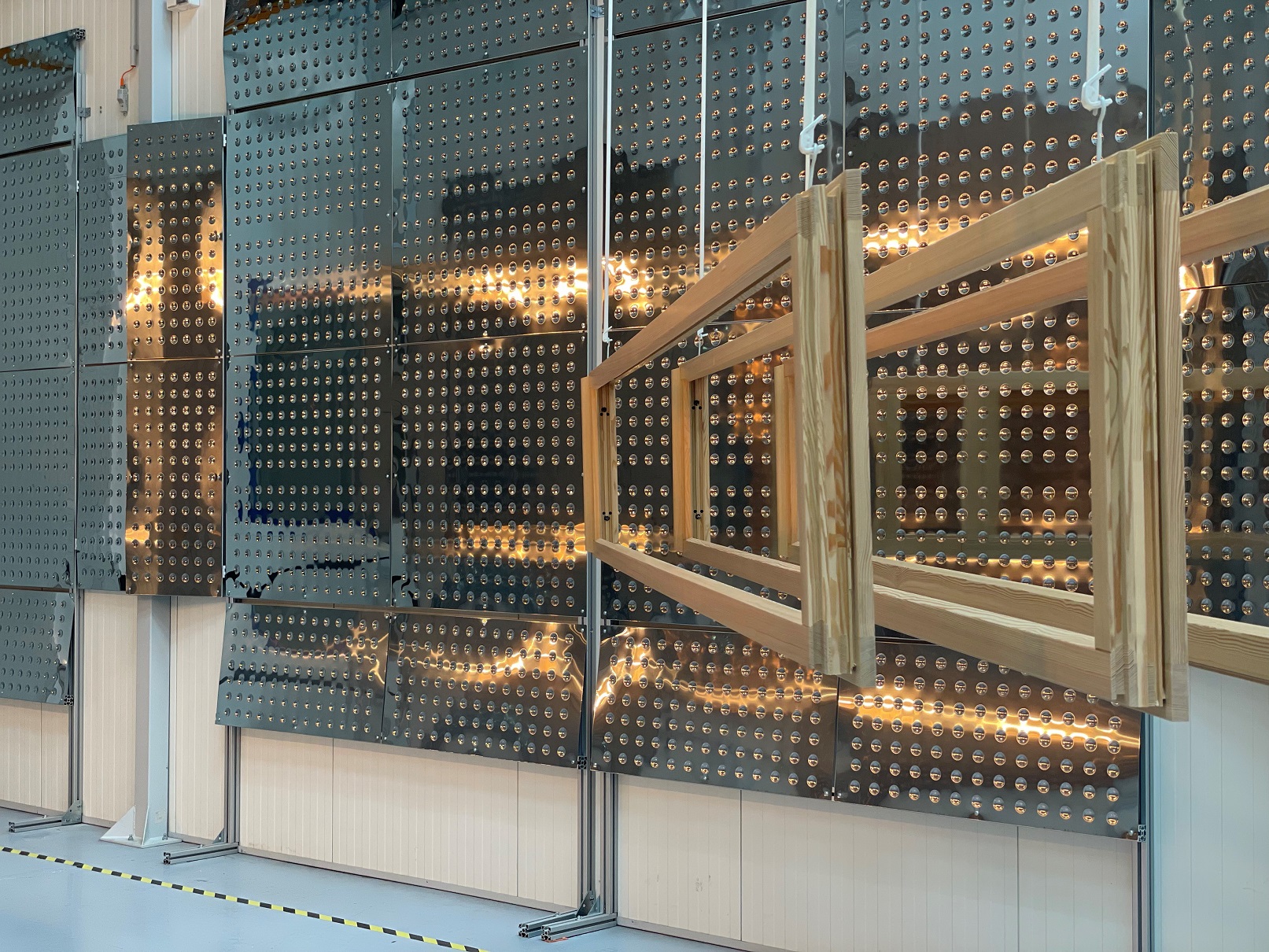
Le séchage infrarouge à coeur s’exécute de l’intérieur vers l’extérieur, il est efficace en 30 minutes au toucher et à coeur en 1h 30.
Avec une température ambiante de 25°C, cette méthode de séchage est 3 fois moins énergivore et ne nécessite pas le refroidissement du tunnel entre chaque menuiserie.
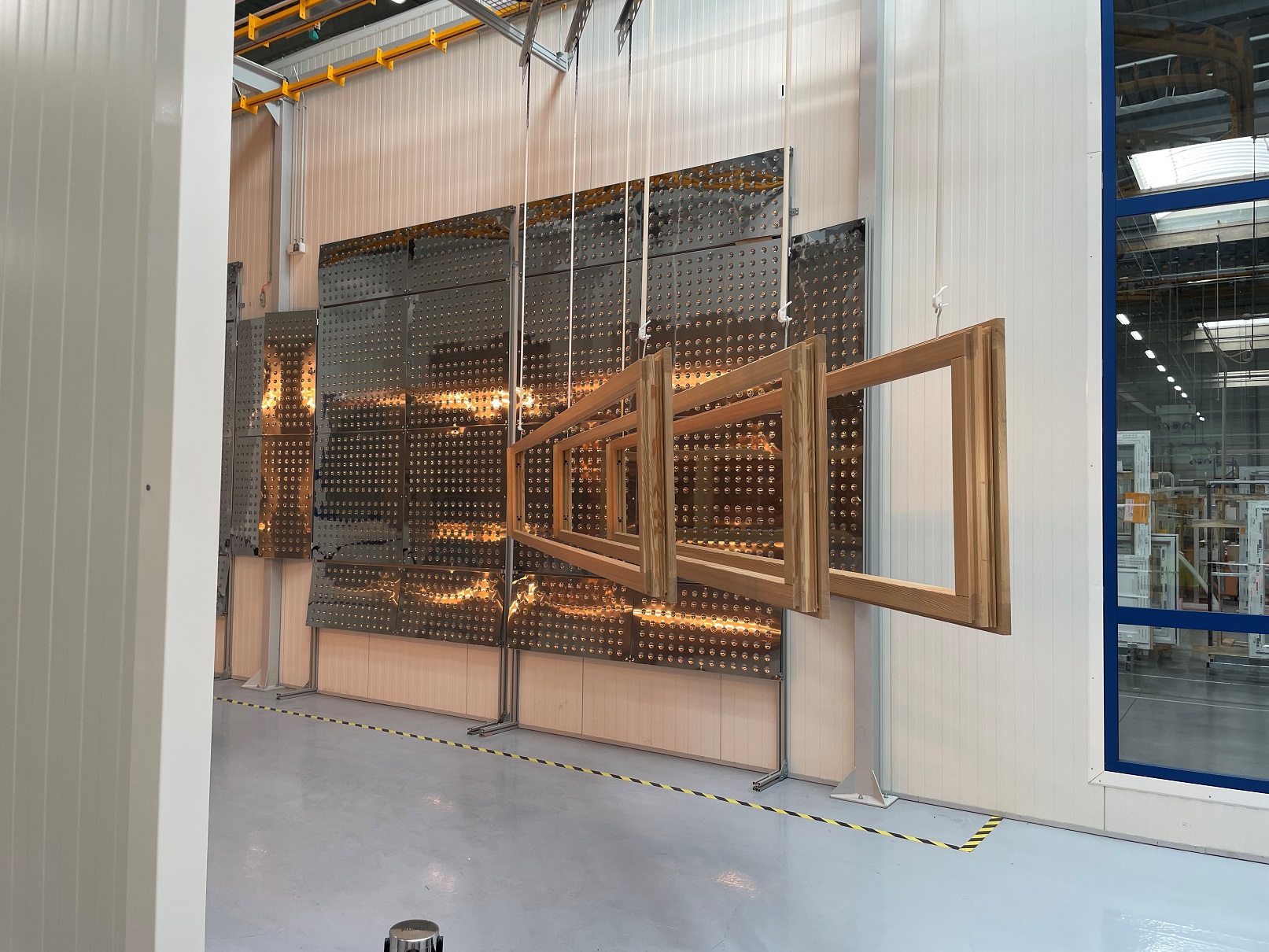
En quelques chiffres, cette nouvelle cabine de laquage ce sont 1000 m² de panneaux sandwich, 25 tonnes d’ossature porteuse, 400 mètres de rail, 750 mètres de chaine avec 8 moteurs d’entraînement, 80 balancelles équipées de puces NFC, 1 menuiserie toutes les 7 minutes.
Mais c’est également et surtout un laquage et un process industriel plus vertueux qui s’inscrivent le cadre d’une stratégie environnementale.
En effet, cette nouvelle technologie de séchage infrarouge à coeur génère un gain énergétique en divisant par 3 la consommation électrique du site.
Outre les mesures déjà mises en place comme l’optimisation des coûts énergétiques du transport et l’approvisionnement de bois issus de forêts gérées durablement, le Groupe utilise des produits classés A+ pour les émissions de Composés Organiques Volatils (COV), recycle les eaux et les boues de peintures de la cabine, exécute un laquage automatisé, précisément dosé et ciblé afin d’éviter le gaspillage et génère des économies de peintures.
Assurément ces process engendrent un gain de productivité mais on le voit, le Groupe Lorillard a également à cœur de réduire son impact environnemental.